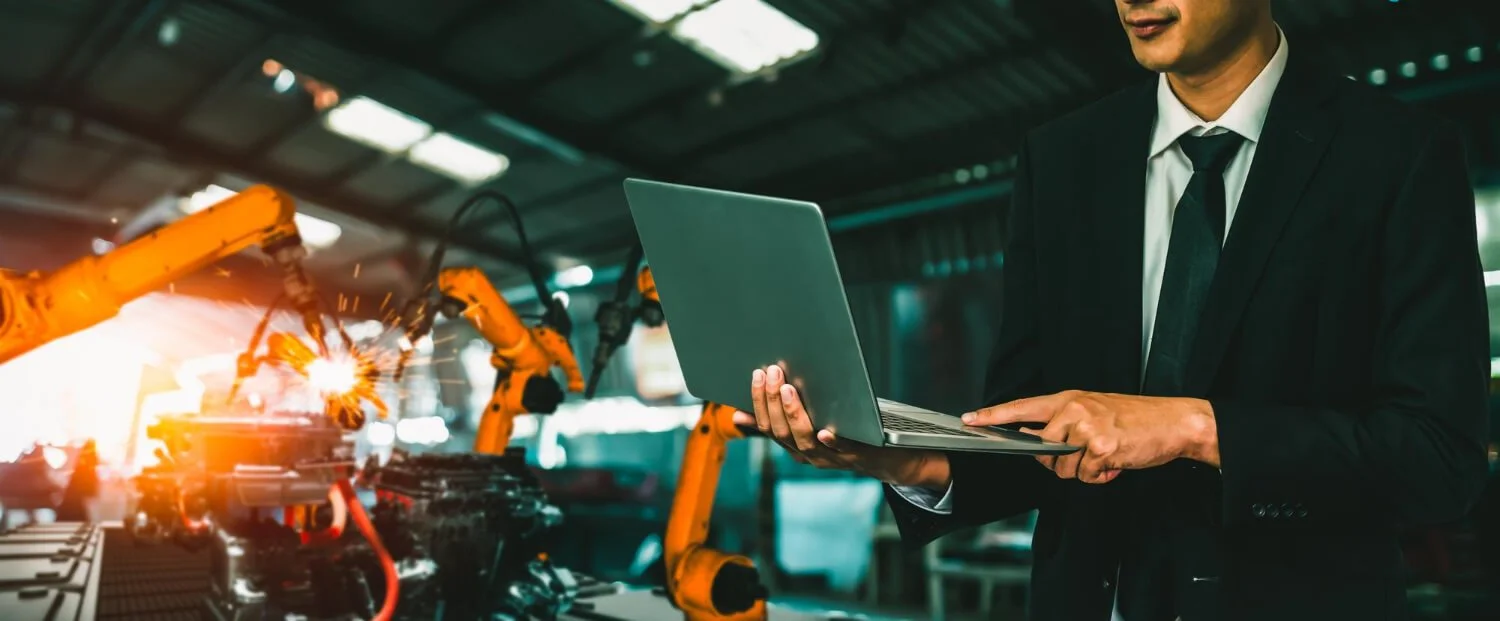
CMMS Implementation Services
In this industry-powered era, where industrial systems have evolved to be more efficient than ever, they have become highly twisted and complicated as well. It can be a nerve-wracking task to maintain these complex processes manually to avoid any unexpected downtime of your machines. That is why it is advised to reap the benefits of CMMS software to stay ahead of the maintenance schedule and eradicate any problems before they occur.
Rildov LLC has been providing proficient CMMS implementation services in the industry for over 20 years. We have a large pool of highly satisfied clients, achieved through the excellence and dedication of our specialists. Contact us to implement CMMS Consulting in your enterprise and streamline the maintenance process.
Do you need help implementing your CMMS Software?
Our CMMS Implementation Process
Phase 1: Planning
Needs assessment to identify maintenance challenges, requirements, and goals to ensure the alignment of CMMS with your organizational needs.
Vendor selection and CMMS evaluation based on user-friendliness, scalability, features and ability to harmonize your existing systems.
Phase 2: Implementation
Data gathering and migration into the new CMMS, including maintenance history, equipment details and spare parts inventory.
Customization of the selected CMMS to ensure its seamless harmonization with the organizational terminology, workflow and other requirements.
Comprehensive training for your maintenance staff on using the system efficiently to ensure a smooth transition and maximum benefits.
Soft implementation of the CMMS in a pilot area to identify and address any potential issues before its full-scale deployment.
Integration with existing systems, such as Supervisory Control and Data Acquisition (SCADA) and Enterprise Resource Planning (ERP).
Phase 3: Go Live!
Rollout and full implementation of the CMMS and onboarding of all the relevant teams to ensure an effective utilization of the system.
Continuous review and improvement to optimize CMMS workflows, maintenance strategies and reports based on performance metrics and feedback.
Send Us a Message
Benefits of CMMS Software in Industrial Maintenance:
Improved Equipment Reliability: CMMS software helps schedule and track preventive maintenance, reducing the likelihood of unexpected breakdowns and improving overall equipment reliability.
Optimized Maintenance Planning: Efficiently plan and schedule maintenance activities based on manufacturers' recommendations, reducing downtime and maximizing asset utilization.
Cost Savings: Identify cost-effective maintenance strategies, optimize spare parts inventory, and reduce overall maintenance costs through better resource utilization.
Enhanced Productivity: Streamline work order management, prioritize tasks, and provide real-time visibility into maintenance activities, leading to increased overall labor force productivity.
Extended Equipment Lifespan: Implementing preventive maintenance schedules and tracking equipment history helps extend the lifespan of critical assets.
Compliance and Documentation: Maintain regulatory compliance by documenting periodic inspections, preventive and corrective maintenance activities, and ensuring that safety standards are met by the maintenance staff.
Inventory Management: Efficiently manage spare parts inventory, ensuring the availability of critical components while minimizing excess stock. Keeping most used and critical parts in adequate stock levels.
Data-Driven Decision Making: Access historical maintenance data and performance metrics to make informed decisions about asset management and resource allocation.
Reduced Downtime: Quickly respond to and resolve equipment issues, minimizing unplanned downtime and disruptions to production.
Enhanced Communication: Facilitate communication and collaboration among maintenance teams, ensuring everyone is on the same page regarding work orders and priorities.
CMMS Implementing Steps:
Needs Assessment: Identify specific maintenance challenges, goals, and requirements to ensure the selected CMMS aligns with organizational needs.
Vendor Selection: Research and select a suitable CMMS vendor based on features, scalability, user-friendliness, and the ability to integrate with existing systems.
Data Migration: Gather and organize existing maintenance data for migration into the new CMMS. This may include equipment details, maintenance history, and spare parts inventory.
Customization: Customize the CMMS to match organizational workflows, terminology, and specific industry requirements.
Training: Provide comprehensive training to maintenance personnel on how to use the CMMS effectively. This ensures a smooth transition and maximizes the benefits of the software.
Pilot Implementation: Implement the CMMS on a small scale or in a pilot area to identify and address any issues before full deployment.
Integration with Existing Systems: Integrate the CMMS with other relevant systems, such as Enterprise Resource Planning (ERP) or Supervisory Control and Data Acquisition (SCADA) systems, for seamless data flow.
Rollout and Full Implementation: Deploy the CMMS across the organization, ensuring that all relevant teams are onboarded and utilizing the system effectively.
Continuous Improvement: Regularly review and optimize CMMS workflows, reports, and maintenance strategies based on feedback and performance metrics.
Maintenance Culture Promotion: Foster a culture of proactive maintenance by emphasizing the importance of using the CMMS for preventive maintenance and timely reporting of issues.
Successful implementation involves collaboration between IT, maintenance teams, and key stakeholders to ensure the CMMS aligns with organizational goals and enhances maintenance efficiency. Regularly reviewing and optimizing processes will help organizations derive maximum value from their CMMS investment.

Many Leading Manufacturers Trust RILDOV LLC to Minimize Downtime
Out team is here to help you!
Benefits of CMMS Implementation
Simplifies maintenance planning and tuning for diverse equipment, streamlining operations.
Provides a visual overview of facility assets with color-coded health indicators for quick assessment.
Eliminates paperwork, automates work order creation, and simplifies task assignments for effective management.
Tracks employee safety data and injury reports, fostering a safer work environment.
Facilitates seamless tracking of material costs and purchase orders for better financial management.
Accommodates work orders from shifting employees or guests, ensuring flexibility.
Automates tasks, reducing reliance on memory and enhancing focus on critical priorities for safety.
Centralizes asset health monitoring, automating preventive maintenance for maximum manufacturing uptime.
Stores user manuals in a mobile-friendly format, making on-site access easy and reducing human error.
Allows for responsible equipment decisions through data tracking and orchestrates safety procedures for regulatory compliance.

Many Leading Manufacturers Trust RILDOV LLC to Minimize Downtime
Out team is here to help you!
Rildov LLC – Where Perfection Meets Excellence
With a 2-decade legacy of exceptional CMMS implementation services and customer satisfaction, Rildov LLC has gained the trust of many clients in the industry. Our distinguishing features include:
Licensed and registered company
A team of qualified experts
Cutting-edge techniques
Competitive cost
Fair communication
Connect with our qualified team today and take a leap towards a smooth and hassle-free industrial maintenance process for your business.
FAQs
-
CMMS (Computerized Maintenance Management System) is a software that helps manage the assets, schedule maintenance and regulate the workflow.
-
No, EAM (Enterprise Asset Management) is a broader system as compared to the CMMS. It can help with financial management, asset management and many other aspects along with scheduling maintenance.
-
CMMS implementation is a complex procedure involving precise execution of many aspects. That is why it is always recommended that certified CMMS implementation consultants be hired for the job.
-
CMMS is not a legal requirement. But it can help you comply with health and safety regulations by regulating work orders and ensuring regular and proper maintenance of the machinery.